A few Fridays ago Terry Herbst, longtime press operator at our shop, retired after twenty years with the company. To give you an idea of his tenure let's note he printed one of our client's newsletters one hundred and sixty five times, and did so without any memorable problems. (Years prior to his stay here, Terry's Army unit in Vietnam also read newsletters that he printed.) Reflecting on Terry's career got me thinking about the things that have changed in our business, and, more importantly, the things that have not.
It's tempting to lump press operators into the larger category of skilled trades such as fabricating or construction. All trades involve the application of basic methods to accomplish the task at hand, but the skills required to run a printing press go further. This is true because of the intangible and fluid nature of the process, and the leap of faith required every time a press operator cranks up on a production run.
The leap of faith is necessary because, at the top of a run, press operators know that they only have limited control over what is going to happen next. Also, that no matter how it goes, they will be held responsible. Those factors that are not under their control include: the quality and personality of the paper; the atmospheric conditions in the shop such as temperature and humidity; the skills of the personnel upstream in the production process; and the fact that wet ink looks different than it will twelve hours later when dry. If you are about to commit $3,000 of the company's paper to a job it takes a lot of guts to push that "RUN" button.
So, what's changed? What makes the life of a press operator different than ten years ago?
The easy answer is digital pre-press and the high quality plates it produces. The elimination of hand assembled film in the platemaking process, and its replacement by laser platesetters, allows for a highly precise process. The plates delivered to the press are cleaner, line up faster, and require less tinkering. All of this gets you to the top of the run quickly; with less frustration and fewer false starts. No operator I know would willingly switch back to the "good old days".
The more complicated trend is the move to all-digital printing, (currently for shorter runs), with no plates at all. These machines are fundamentally different than conventional offset presses.
This leads to a conundrum in the operator's life, because it upsets the balance between art and science. (By art I refer to skill based on intuition.) There is much less interaction between the machine and the operator, and finely tuned adjustments cannot be made during the run. This could relegate the operator to the role of "mouse jockey", but fear not; here comes the basic fact which will never change.
Customers care deeply about the quality of work they receive. (I learned this firsthand at a print shop where I made all my own customer deliveries.) In order for the high-fives and victory lap to commence a lot of people have to do a lot of things right...and key to that success are the tradespeople who put the image down on the sheet. Any tradesperson "worth his salt" knows that the customer will scrutinize the work, and takes the steps necessary to be proud of what goes out the door.
This pride has always been the source of good tradecraft. Regardless of the level of technology, high quality work comes from equipment that is well cared for, run by people who give a damn about what they're doing. The knowledge that their extra effort make a difference, and that the customer deserves it, is what distinguishes a tradesperson from someone just punching the clock.
With sincere thanks to Terry for his millions of good impressions, and best wishes to him and Linda in the years ahead,
Hugh Butler
Your friend in the printing business
Friday, April 23, 2010
Monday, April 5, 2010
New Technologies and the Hype Cycle
The commentary cloud surrounding social media has made much of the "Hype Cycle" of new technology. I thought it would be helpful to place some printing technologies along this curve. Because this blog strives for original content, certain liberties have been taken with the following graphic explanation:
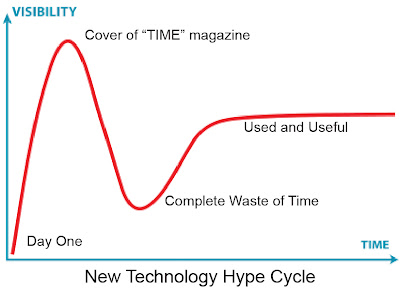
Our business has brought several new technologies into the mainstream with significant benefit to our customers. They're evaluated here in no particular order:
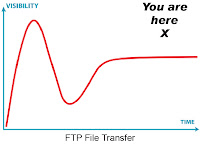
FTP File Transfer: File Transfer Protocol, or FTP, is a fully mature method of communicating production files to a print shop. Depending on their client profile printers use a dedicated FTP server, providing secure access to a client area, or a browser based system. Either way, files too large to email efficiently can be sent to or from the shop. For people like me, who used to have to drive everywhere to pick up disks, this technology is invaluable, and customers benefit from the ability to get their job inside the shop in minutes. If your printer doesn't offer FTP, clients can do it themselves by using services such as box.net or yousendit. My yousendit dropbox, for example, is here and requires no special software, login, or password.
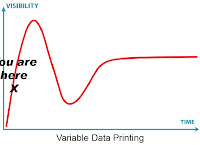
Variable Data: "Mail Merge" on steroids, this technology has run out in front of user demand, and is often present in a local printing market just waiting for people to catch on. Digital printing technology makes the inclusion of customized data in a printed piece relatively easy, and usually ties that component into a larger campaign. Offer numbers, customer numbers, product keys, customer names, postal addressing, and various security features are all capable of being incorporated; all that is required is imaginative thinking and collaboration with your provider.
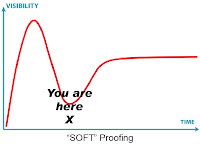
Soft Proofing: a/k/a onscreen proofing is a great way speed up and economize the approval process assuming the following: 1) You are a fastidious proofreader before submitting your file to the printer and 2)have trained everyone in your office to be the same. 3) You are a technical super-pro with a longstanding track record, and 4) a compulsive gambler. All the rest of us mortals should stick to hardcopy proofing. I personally do not know anyone who can proofread onscreen to a level which can guarantee a project will be error free. I know this to be true because I see our customers spend thousands of dollars correcting simple editing errors which are only caught in hardcopy form at our proof stage.
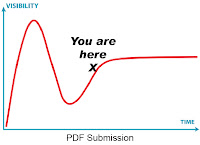
PDF submission: Most commercial shops use PDF based workflow systems because of their compact and reliable nature. Since the individual pages which make up your layout are going to be converted to PDF anyway customers can (and sometimes must) perform that step themselves and simplify file submission. There are a few common problems, however, which will fill you with a sense of rejection; most important, the file must be created with all fonts embedded.
The defining feature of a PDF file is its ability to render properly no mater which computer it’s on. Key to this ability is the file’s willingness to carry within itself a copy of all the fonts which were used by the original program (Word, InDesign, etc). Unfortunately, this feature can be defeated by the home computers desire to keep the file size small, and thus omit the internal font copies. It is imperative that the settings used to create the PDF instruct that the fonts be “embedded” or else the file will, without warning, substitute whatever fonts may be available in its new neighborhood. This can cause problems ranging in size from troubling to disastrous.
The solution is simple and easy to check. First, use the “Press Quality” settings from the menu at the PDF creation step. (For Microsoft products also be sure the “never embed” window is empty.) Second, after the file is created, go to File>Properties>Fonts to be sure ALL fonts listed are followed by the term “embedded subset” as in the following picture.
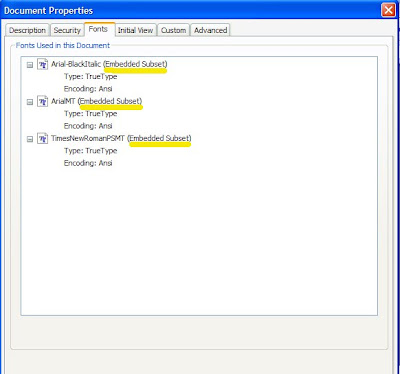
Second most important, the file must allow for extra image outside the trim size of the file if the printed image “bleeds” off the edge. My dog, Lassie, will now demonstrate, although you should click on the picture to see it full size:
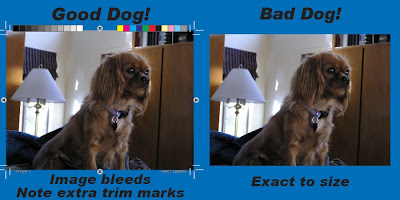
Third most important, check to see that you ended up with the colors you intended for printing. The step in Acrobat is Advanced>Print Production>Output Preview and you'll see something like the following, and there is NO END of interesting details you can learn about your file:
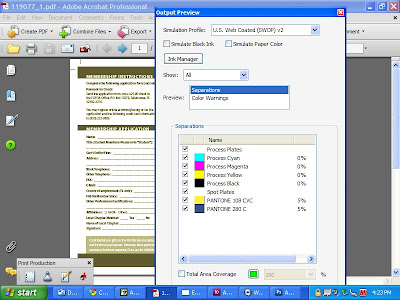
I'm happy to return to this page after a two month hiatus during which the actual printing business was quite hectic. Many wishes came true at our shop, with the result being my neglect of you loyal readers. I hope the first quarter of 2010 was encouraging for you as well, and look forward to your feedback online.
Sincerely,
Hugh Butler
Your Friend in the Printing Business
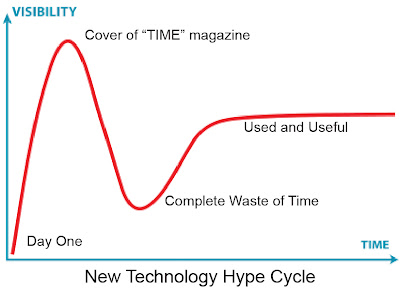
Our business has brought several new technologies into the mainstream with significant benefit to our customers. They're evaluated here in no particular order:
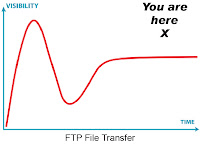
FTP File Transfer: File Transfer Protocol, or FTP, is a fully mature method of communicating production files to a print shop. Depending on their client profile printers use a dedicated FTP server, providing secure access to a client area, or a browser based system. Either way, files too large to email efficiently can be sent to or from the shop. For people like me, who used to have to drive everywhere to pick up disks, this technology is invaluable, and customers benefit from the ability to get their job inside the shop in minutes. If your printer doesn't offer FTP, clients can do it themselves by using services such as box.net or yousendit. My yousendit dropbox, for example, is here and requires no special software, login, or password.
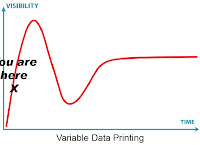
Variable Data: "Mail Merge" on steroids, this technology has run out in front of user demand, and is often present in a local printing market just waiting for people to catch on. Digital printing technology makes the inclusion of customized data in a printed piece relatively easy, and usually ties that component into a larger campaign. Offer numbers, customer numbers, product keys, customer names, postal addressing, and various security features are all capable of being incorporated; all that is required is imaginative thinking and collaboration with your provider.
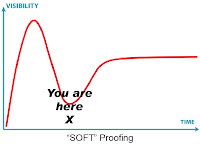
Soft Proofing: a/k/a onscreen proofing is a great way speed up and economize the approval process assuming the following: 1) You are a fastidious proofreader before submitting your file to the printer and 2)have trained everyone in your office to be the same. 3) You are a technical super-pro with a longstanding track record, and 4) a compulsive gambler. All the rest of us mortals should stick to hardcopy proofing. I personally do not know anyone who can proofread onscreen to a level which can guarantee a project will be error free. I know this to be true because I see our customers spend thousands of dollars correcting simple editing errors which are only caught in hardcopy form at our proof stage.
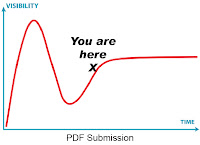
PDF submission: Most commercial shops use PDF based workflow systems because of their compact and reliable nature. Since the individual pages which make up your layout are going to be converted to PDF anyway customers can (and sometimes must) perform that step themselves and simplify file submission. There are a few common problems, however, which will fill you with a sense of rejection; most important, the file must be created with all fonts embedded.
The defining feature of a PDF file is its ability to render properly no mater which computer it’s on. Key to this ability is the file’s willingness to carry within itself a copy of all the fonts which were used by the original program (Word, InDesign, etc). Unfortunately, this feature can be defeated by the home computers desire to keep the file size small, and thus omit the internal font copies. It is imperative that the settings used to create the PDF instruct that the fonts be “embedded” or else the file will, without warning, substitute whatever fonts may be available in its new neighborhood. This can cause problems ranging in size from troubling to disastrous.
The solution is simple and easy to check. First, use the “Press Quality” settings from the menu at the PDF creation step. (For Microsoft products also be sure the “never embed” window is empty.) Second, after the file is created, go to File>Properties>Fonts to be sure ALL fonts listed are followed by the term “embedded subset” as in the following picture.
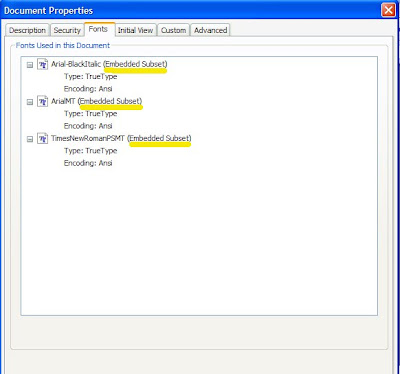
Second most important, the file must allow for extra image outside the trim size of the file if the printed image “bleeds” off the edge. My dog, Lassie, will now demonstrate, although you should click on the picture to see it full size:
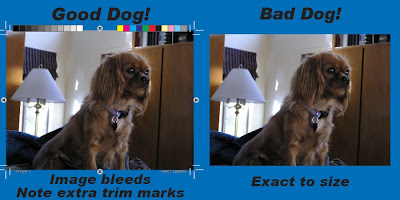
Third most important, check to see that you ended up with the colors you intended for printing. The step in Acrobat is Advanced>Print Production>Output Preview and you'll see something like the following, and there is NO END of interesting details you can learn about your file:
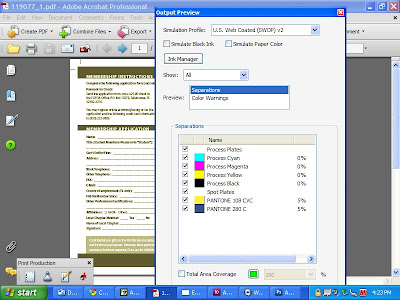
I'm happy to return to this page after a two month hiatus during which the actual printing business was quite hectic. Many wishes came true at our shop, with the result being my neglect of you loyal readers. I hope the first quarter of 2010 was encouraging for you as well, and look forward to your feedback online.
Sincerely,
Hugh Butler
Your Friend in the Printing Business
Subscribe to:
Posts (Atom)