Wednesday, November 26, 2008
Happy Thanksgiving
Friday, November 21, 2008
Lost in translation
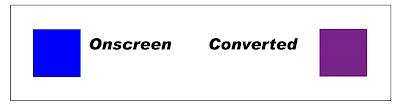
By Dan Margulis
Published by Peachpit Press, 2006
ISBN 032144017X, 9780321440174
Friday, November 14, 2008
I think I want, you know, like, the shiny paper?
To my understanding "matte" is usually used to describe paper with a dull finish. It is often confused with uncoated paper, but you can actually have a "matte" coating that is still dull in appearance. She then goes for the extra credit points by discussing matte finishes which can be applied after the regular inks go down, but we're limiting our discussion to the paper itself.
The key distinction when describing paper is whether it's coated or uncoated. It's at this point that the term "matte" often jumps in and, as Shelley points out, what people may mean is uncoated as opposed to a coated stock with a matte finish. If you don't know whether the paper you have in mind is coated or uncoated you stand almost no chance of communicating effectively what you are looking for. This is something you REALLY need to know. Here are the details which, for once, are relevant:
The ingredient in the mix which provides the coated aspect is clay (in addition to the routine pulp which all paper contains) providing a much harder, more reflective surface as the mix is rolled out in the paper mill. The coating (or absence of coating) changes radically the amount of light the sheet reflects. Printing inks are transparent...light passes through them and bounces off the paper, and the more light that bounces back the more light energy strikes your eyeball. The more your eyeballs are stimulated by this light the brighter your colors appear. The same ink film printed on coated and uncoated stock will appear as two completely different colors. Beware.
This is relevant in two ways; first because you want to predict what your colors will look like and second because you want to be sure you can describe the paper to be quoted.
Your colors should be previewed by checking them against a Pantone (or similar) printed reference book. (The Pantone.com link is on my main page for reference.) All of these terrific guides come in a coated and uncoated version...if you buy printing regularly, and you don't have them you are an accident waiting for a place to happen. But what if you need a preview of an image where there is no single color applied such as a color photograph or full color graphic?
In such a case, hopefully, your print vendor will supply your color contract proof on an uncoated material; if not you will need some considerable guidance from them about what shifts will transpire when the image is printed. In my experience, printing full color (CMYK) on an uncoated stock will often lead to colors which disappoint the customer, unless a muted effect is desired. It doesn't mean that the paper has to be glossy, but most often a coated stock seems preferable.
Here are your choices, (and we're finally going to get to the "matte" term in it's correct context).
COATED STOCKS: In descending order of "shininess".
Cast Coated text and cover, high mirror gloss, expensive, specialized, easy to confuse with regular gloss which has an extra top coating of gloss laminate, varnish, or UV applied by the printer (not native to the paper itself).
Gloss coated text and cover, nice and shiny, clean color, fast drying, little show through.
Dull coated text and cover, same as above but less shiny, easier to read, non glare surface, can be written on, sometimes needs an extra day dry time.
Matte coated text and cover, least shiny, most texture, quality varies A LOT, drying of ink often unpredictable. We're not crazy about it.
UNCOATED STOCKS
Book paper; Offset and opaque offset, similar to varying grades of paper for your copier or laser printer, inexpensive, low weight (for mailing).
Textured and Textured Cover; Available in a wide range of colors, textures and weights, great tactile properties, sometimes availability problems.
Writing papers; 25% cotton usually with a watermark for use as letterhead, envelopes and matching cards for stationery packages. It isn't cheap but the high level of quality is usually worth it for personalized written communication.
Index, tag, bristol; specialized uses for cards, tags, el cheapo postcards.
So there you have almost the entire universe of printing papers if you can remember eight basic grades. You don't need to know the paper business inside out, but these terms are important. Swatch books are available for typical brands and your vendor can help with the (unbelievably arcane) system of weights which apply. It's much more impressive to say "I want it on gloss text" than to resort to "I think I want, you know, like, the shiny paper?"
I appreciate the responses to last weeks question so much I'm going to use the same approach to gather information for next week. A reader asked about preventing color shifts when going from RGB on her monitor to printed CMYK color. Particularly skin tones which come out looking like the subject has a high fever, and blues which pick up a lot of magenta and say "HELLO, I'M BARNEY THE DINOSAUR"! Any responses will be combined with my own meager knowledge for next weeks post, and one name will be drawn from those who reply for the Atlanta Bread Company goodies. Let's see how much expertise we have out there among you PhotoShop experts.
Until then , see you online!
Hugh Butler
Your friend in the printing business
Friday, November 7, 2008
Gone WRONG, part II
Last week, in honor of Halloween, we suffered through problems with print quality and issues surrounding the printer's proof. This week we continue our bad luck with shortages and delivery. Finally, we'll search for the redemption of understanding in how how to approach these pitfalls, and then be able to move on to more cheerful topics.
Shortage problems: By tradition in the printing business, a delivery of 10% over or under the requested quantity constitutes completion of the order with the invoice pro-rated to reflect the actual amount. (There are actually good reasons why this is so.) By this logic an order for 1000 newsletters is considered complete if the vendor delivers 901 and bills you for that many. For many customers this may be unacceptable, but in the absence of an agreement it's likely what your vendor is thinking. What if your mailing list has 950 names?
Solution: Like so many things we'll discuss, the difference between a deal and a dispute is what you agree to in advance. If the exact quantity is critical specify the order as "1,000 copies, no unders". You will pay slightly more; this is because the vendor will need to purchase some extra stock to guarantee the count even if a small problem is discovered after the presswork is complete. If, however, the count comes up short there will be no dispute about the vendors responsibility to put the job back on the press. The main point is to have a clear understanding with the printer BEFORE the issue comes up.
Hint: Shortage problems often come up when the job is being processed at a mailer. Several possibilities exist; the printer's count may be short, the mailer may have spoiled or misplaced part of the order, or your mailing list may have more names than you anticipated. My first post addressed this last issue (see This will be Win-Win) and if you're joining this blog recently you may want to go back and read it in the archive.
Delivery Problems: Here your job is delivered late, to the wrong destination, or in a manner unsuitable for the destination, (think tractor-trailer showing up at plush office with no loading dock).
Solutions: If any aspect of the delivery is critical that information must be part of the original job specs. If it is then missing from the printers proposal, that fact should be corrected before acceptance, and be stated clearly on any purchase order. It's vital that this kind of information be conveyed (or at least confirmed) in writing and as early as possible in the process.
Hint: There is a WORLD of difference between "I need it next Monday" and "I need it next Monday by 8:30 AM when my boss will present it at a meeting in Tampa". If a delay of one day renders the product unsatisfactory, you need to be clear in advance that's the case and have an agreement about possible contingencies. It is unreasonable to make a claim for delay if information has been withheld and the job is proceeding on a "normal" schedule. Likewise, the vendor must be honest about the progress of your job, and if a delay becomes apparent may need to consider what steps must be taken to avoid a breach of their responsibility.
OK, let's restart the clock and call the vendor to discuss what happened and how to proceed. If the situation is clear cut, hopefully the party involved will own up to their responsibility. If responsibility is not so clear, hopefully the two parties will remember the value of their continued relationship and work to resolve the issue in a way which is mutually satisfactory.
Effective communication before the fact will prevent many..Blah, Blah, Blah, Blah.
You knew I was going to say something like that, and it's true. Just as true, however, is that things go wrong in a fast paced environment like a printshop. Things will also go wrong as long as customers have ten zillion other things to concentrate on besides their printing. When things go wrong after ink is on paper the cost of remedies are substantial, which is why we stress our mutual efforts BEFORE that crucial step has occurred.
Your best idea is to try and understand what's going on in the other person's world, and be aware of how they look at your common goal. If, then, you're clear about YOUR role in the process you can concentrate on doing the best possible job of dotting the "i"s and crossing the "t"s. That way you can open up the box and say "There! Now THAT'S what I expected"!
Here's a question related to next weeks post for your consideration: What does the term "matte" refer to specifically in the printing trade? I'll draw one name at random from any correct (or even close to correct) responses to receive an order of muffin tops from the Atlanta Bread Company, delivered personally by yours truly.
Thanks for stopping by!
Hugh Butler
Your friend in the printing business